Blog
Read our blog to stay up to date with the latest Cyber Security trends, best practices, new product features, and emerging threats to protect your industrial systems.
Decoding NERC CIP Series | Vulnerability Tools to Simplify Patching
This article is part of our ongoing podcast blog series, where we explore the practical challenges...
ICS Critical Patch Updates: June 2025
Welcome to Foxguard’s ICS Critical Patch Updates June 2025, your go-to monthly resource for...
ICS Critical Patch Updates: May 2025
Welcome to Foxguard’s ICS Critical Patch Updates May 2025, your go-to overview of the top...
Decoding NERC CIP Series | OT Patching Solution Challenges
This article is part of our ongoing podcast blog series exploring practical challenges and key...
Decoding NERC CIP Series | Asset Identification
Welcome to the first blog in our new series on NERC CIP compliance and OT security! This blog...
ICS Critical Patch Updates: April 2025
Welcome to the April edition of Foxguard’s ICS Critical Patch Updates, your go-to resource for...
ICS Critical Patch Updates: March 2025
Welcome to the March edition of Foxguard’s ICS Critical Patch Updates—your monthly resource for...
Patch Now, Next, or Never: OT Cyber Security & NERC CIP
Patching an Operational Technology (OT) environment poses unique challenges that are rarely a...
ICS Critical Patch Updates: February 2025
Welcome to the February edition of Foxguard’s ICS Critical Patch Updates—a monthly series designed...
Get exclusive updates by joining our email list
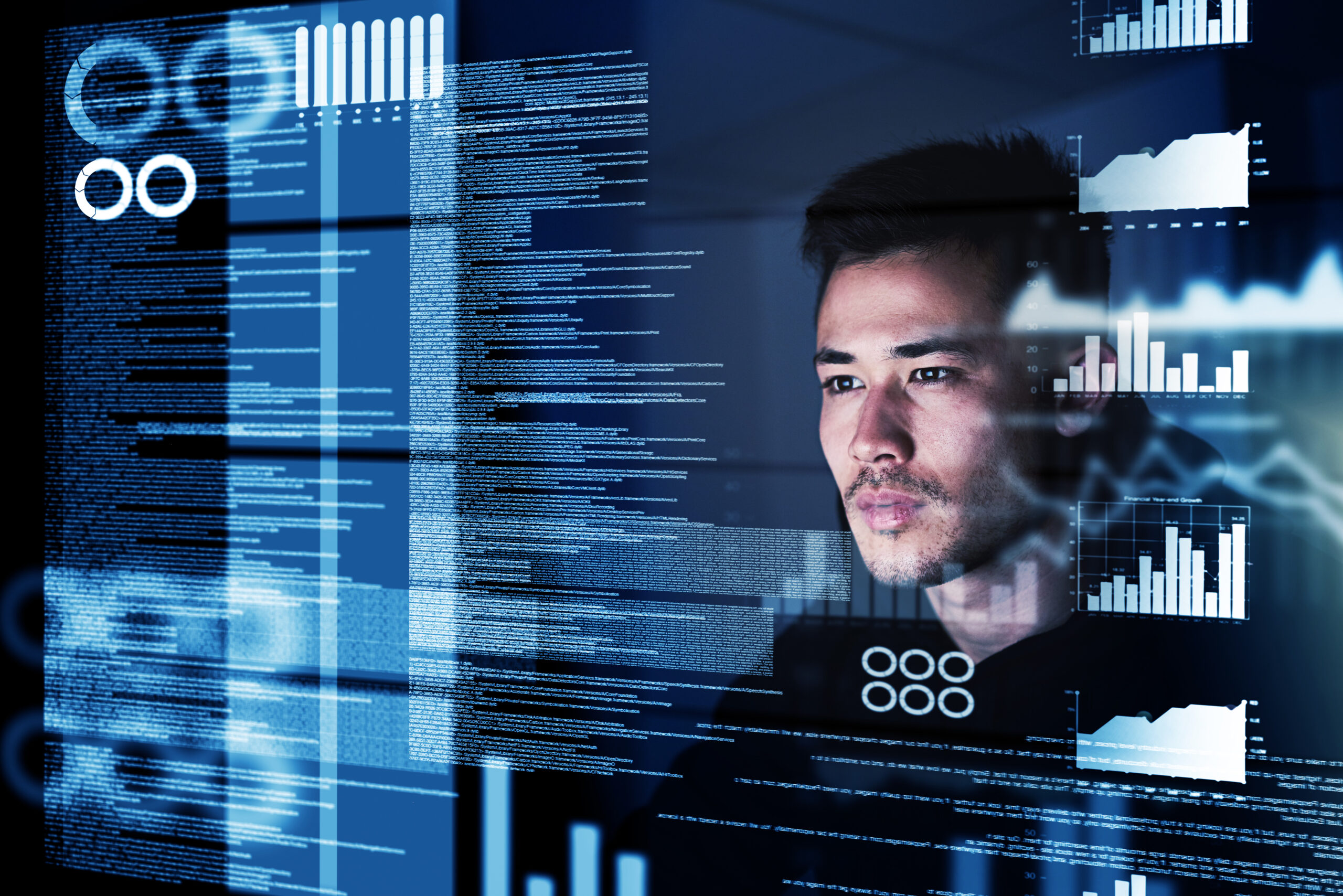